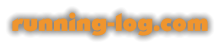
September 19, 2013 (Afternoon)
Exercise Type: Run
Comments:
Started today at the caster to watch startup. That was incredible. The team of 5 guys worked like an incredible machine. They all knew exactly what needed to happen at exactly the right time and worked together seemlessly. Honestly one of the coolest things I've seen here. It was very much a hurry up and wait type deal. We waited for a couple hours in the morning while the LMF fixed some of the troubles it had been having coming back on line after the shut down. But once the time came it was a furious 45 minutes.
Start up was one of the things the mystified me most about continuous casting steel making. I understood the basic process but didn't really understand how one would get it started. What happens is that dummy bars are inserted into the bottom of each mold. These grab onto little formed rectangles of steel. They are hollow on one end and formed so that the dummy bar can grab them on the other. When the steel is first poured into thse rectangles it effectively welds its self to the steel piece. The dummy bar then pulls it through the process until at the bottom rollers disengage it from the dummy bars. The first billet is scrapped but everything after that is good to go. Thas lack of scrap is particularly amazing.
So after the caster was up running smooth again I went down to the torch pit which is the last step in the melt shop process. Here the billets get cut to length, changes in grade are very important here as well.
Mostly the torck pit just cuts the billets to length and marks where one heat begins and the other begins. They know this from a computer that calculates how many billets per strand will come from each heat based on the casting rate and data from the caster on when they change heats. They take samples from the first billet and last billet of each strand every heat to ensure that the internal quality of the billets is up to specification.
When things get ineresting is a grade change. Since casting happens continusouly, there are two different grades of steel present in the tundish. This leads to mixed billets when this steel reaches the tourch pit. The computer system calculates where this mixed zone begins. A bit before that point the tourch pit opperator cuts billets free from every strand. Then as these mixed billets come out samples are taken from the end of each billet. These samples are tested for chemistry. When the chemistry from all four starnds is the same the opperator knows that the grade change is complete and good billets are again produced. The mixed billets are usually labled "no grade". These are used for trials in the rolling mill, since they can't be sold it doesn't matter if they get messed up when the rolling mill wants to try out a new process.
Unfortanatly I was only in the tourch pit for like 2 hours before I had to go back to cold finish. I got to see a grade change though which was cool. Then I rolled out back to cold finish. There I caught up with Marc on what went on and what will happen next week when he's away recruting interns.
I get most of the day off tomorrow. That's nice. Wrap up to a solid week in the melt shop.
Distance | Duration | Pace | Interval Type | Shoes |
---|---|---|---|---|
4.0 Miles | 29:56 | 7:28 / Mile | Easy | GTS 13 Blue |